Precast concrete is not used as much in residential construction as in commercial development, but that could be changing.
By Susan Bady
While the predominant structural material for single-family houses is still wood, builders are recognizing the merits of precast concrete in making homes more durable, low maintenance, and energy efficient. Precast is a big time-saver in the field and can also be a big money-saver. The key to a successful project lies in getting a precast concrete producer on board early to collaborate with all the key players, including the architect, contractor, developer, engineer, and client.
Precasters can produce a diversity of colors, textures, and custom components to ensure that the finished product is anything but bland and boring. Precast floor planks create long spans that would not have been possible with wood floor joists, allowing for large open spaces. Because they are made in the factory, precast components offer more consistent quality control than cast-in-place concrete. Moreover, precast is fire resistant and impervious to insects, and can stand up to extreme weather, making it an attractive choice for hot, humid climates and areas prone to hurricanes, wildfires, floods, and other disasters.
“I’ve been using more and more off-site fabricated components over the years, and I expect that trend to continue,” says builder Josh Wynne of Josh Wynne Construction, Sarasota, Fla. Wynne has extensive experience with precast concrete, from more common pieces like sills and lintels to more structural components such as hollow core panels, and finish items such as precast concrete countertops, fireplace surrounds, and tiles. He installed precast counters as well as sills and lintels in Rancho da Florida, a custom home in Myakka, Fla., that won a Platinum award in the 2019 BALA competition.
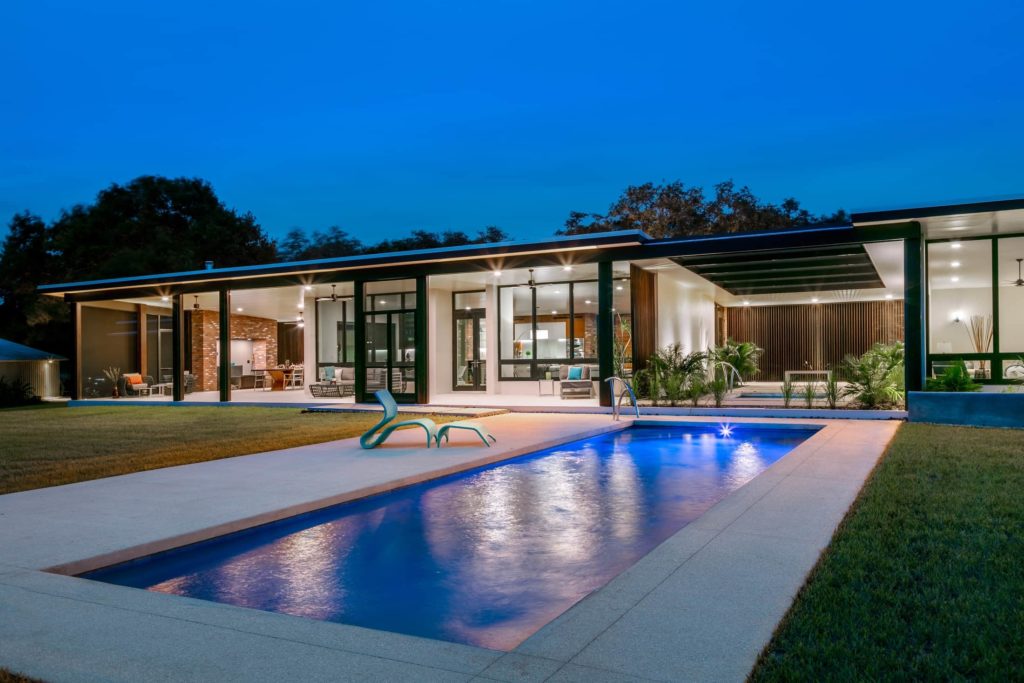
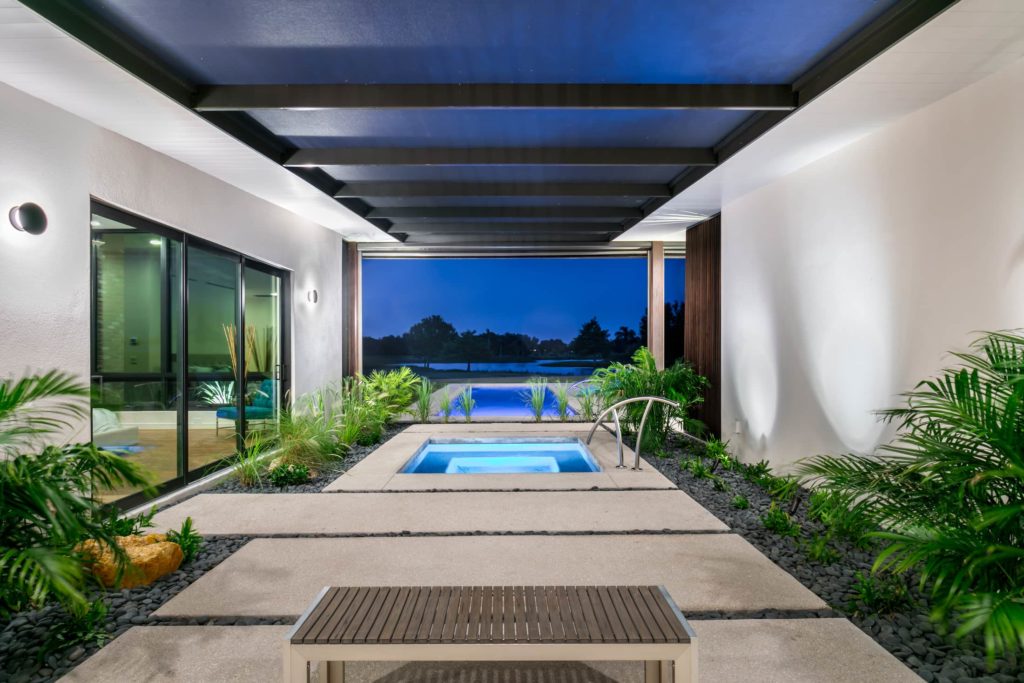
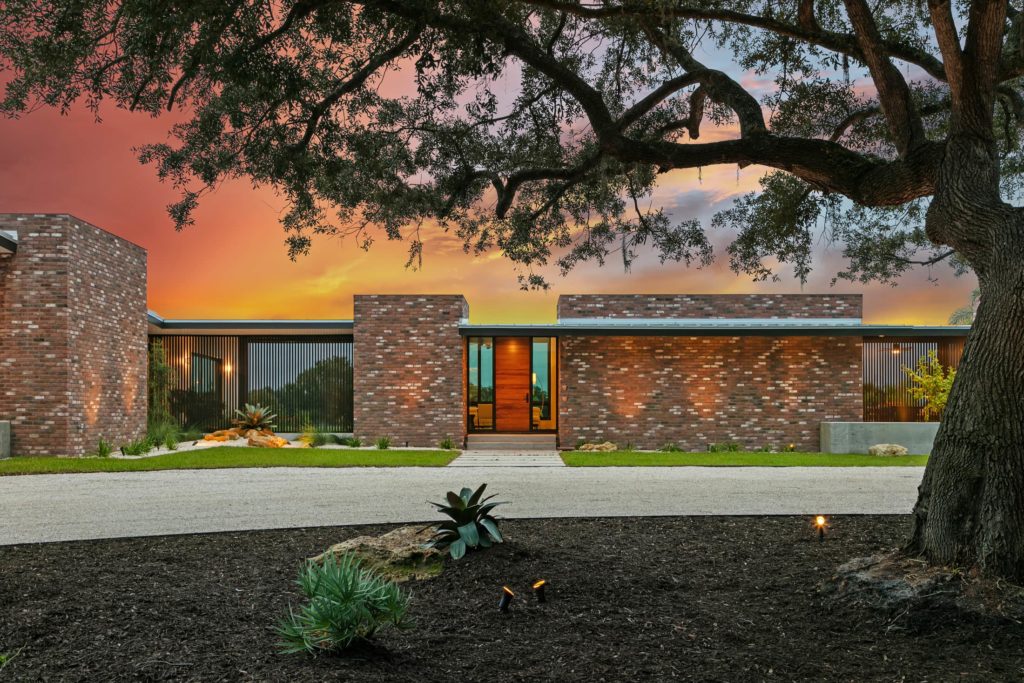
Chapel Hill, N.C., architect Arielle Schechter, PLLC, AIA, likes to use a precast concrete wall system in the homes she designs “because it combines customization within the prefab process. The walls are fabricated by a local company one town away and they don’t mind that I use custom window sizes and custom wall heights.” Because the walls go up so quickly, the house can be dried in faster, saving on labor costs.
Schechter says her clients also like the precast system because the walls are completely termite resistant, the exterior is low maintenance, and the concrete offers greater fire resistance than wood framing.
“[And] there is a thrill factor of seeing their exterior walls go up via crane in two days,” she adds.
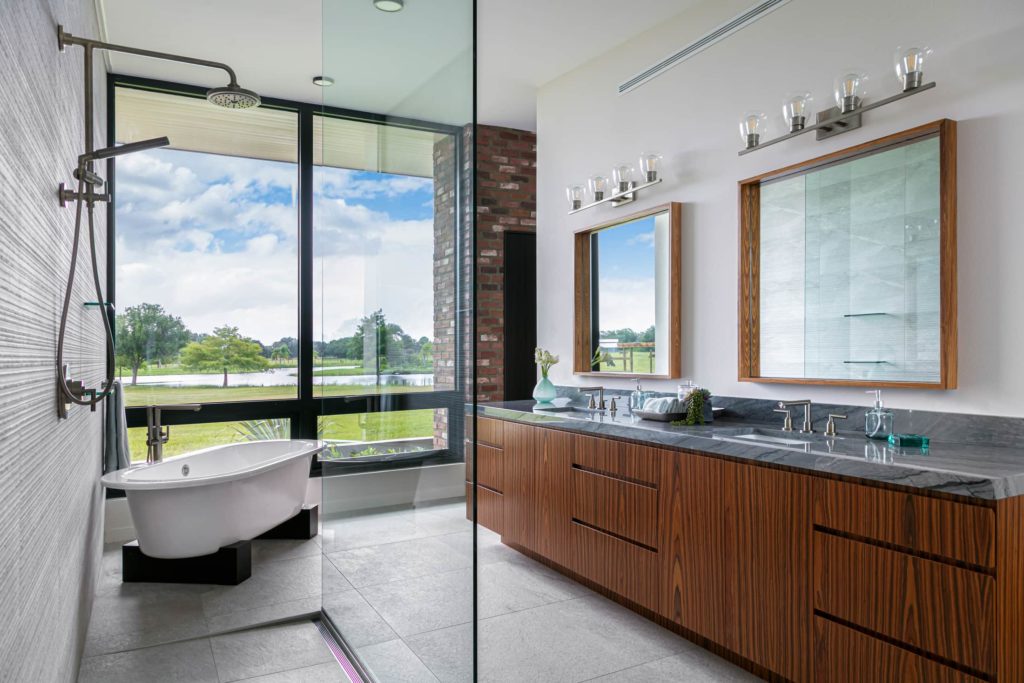
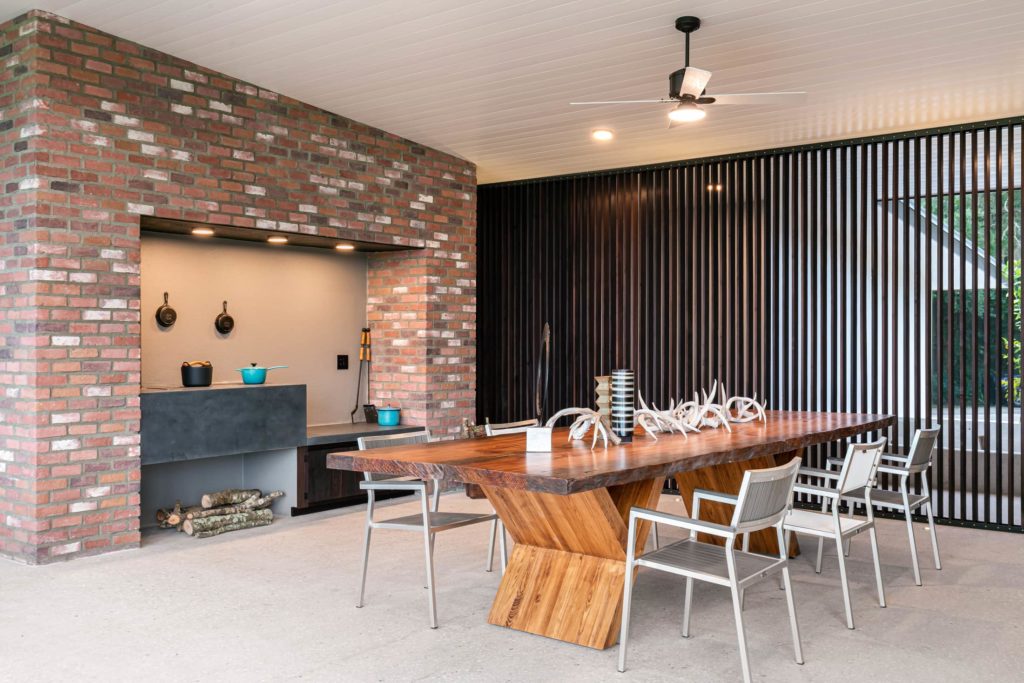
Quick Assembly, Low Upkeep
Speed of assembly is assured with precast concrete because the components are fabricated off site. A 4,755-square-foot oceanfront home in La Jolla, Calif., designed by Domusstudio Architecture and built by Premier Custom Builders, both in San Diego, features precast concrete wall panels that were made in the factory, delivered to the site, and erected by crane in a single day. The spine of the home is articulated with these exposed concrete panels, says Domusstudio principal John Pyjar, AIA, LEED AP.
The thin structural wall panels were made by pouring 2-1/2-inch thick concrete into a frame made of light-gauge metal and letting it cure. The manufacturer, StructureCast, claims that the panels far exceed minimum seismic, sound, fire, and wind requirements.
While the panels were challenging to install because the structural connection points are hidden in dual-sided panels that are capped at the top and ends, Pyjar was happy with the end result, which he says has the look and finish of poured concrete.
Because the manufacturing is done off site, precast concrete components are a good solution for narrow or tight lots where it would be difficult, if not impossible, to fit cement-mixing trucks.
GRO Architects, New York, N.Y., developed the PREttyFAB prototype house using precast concrete insulated panels. According to the architects, PREttyFAB, which won a Design Award for Best Single-Family Home from the Precast Concrete Institute, precast enabled them to develop complicated geometrical details and was less problematic in terms of satisfying the insulation needs of the Jersey City, N.J., climate.
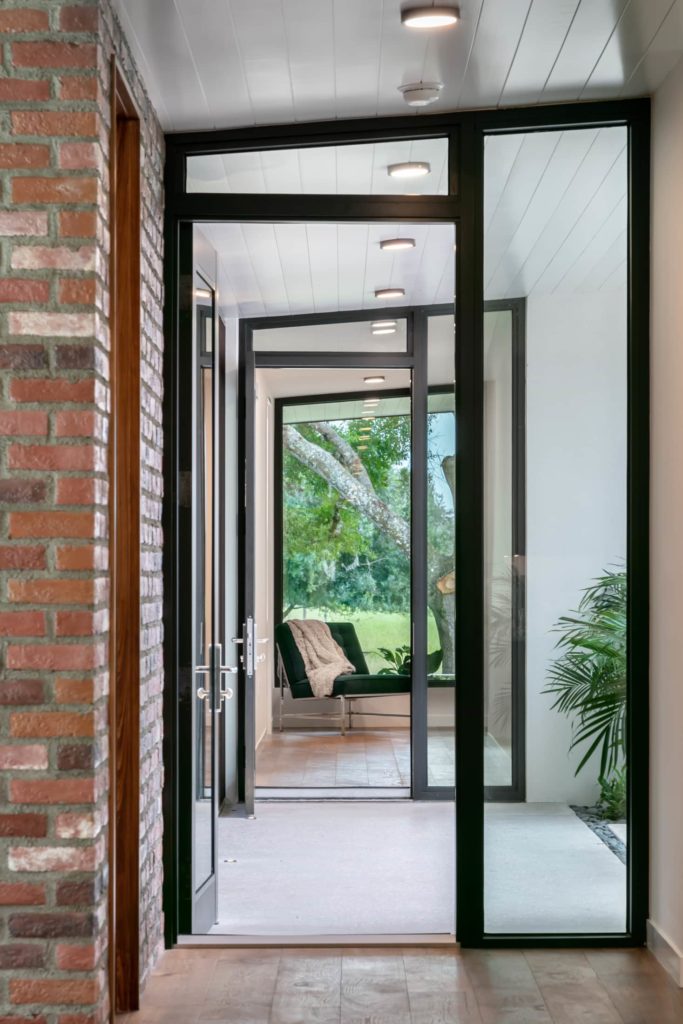
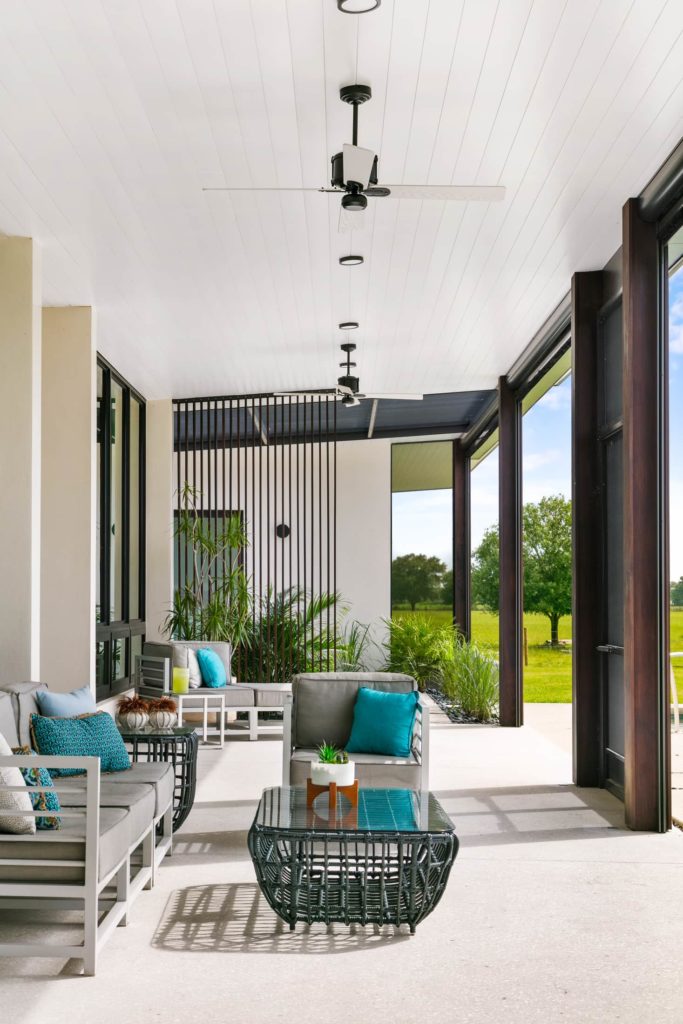
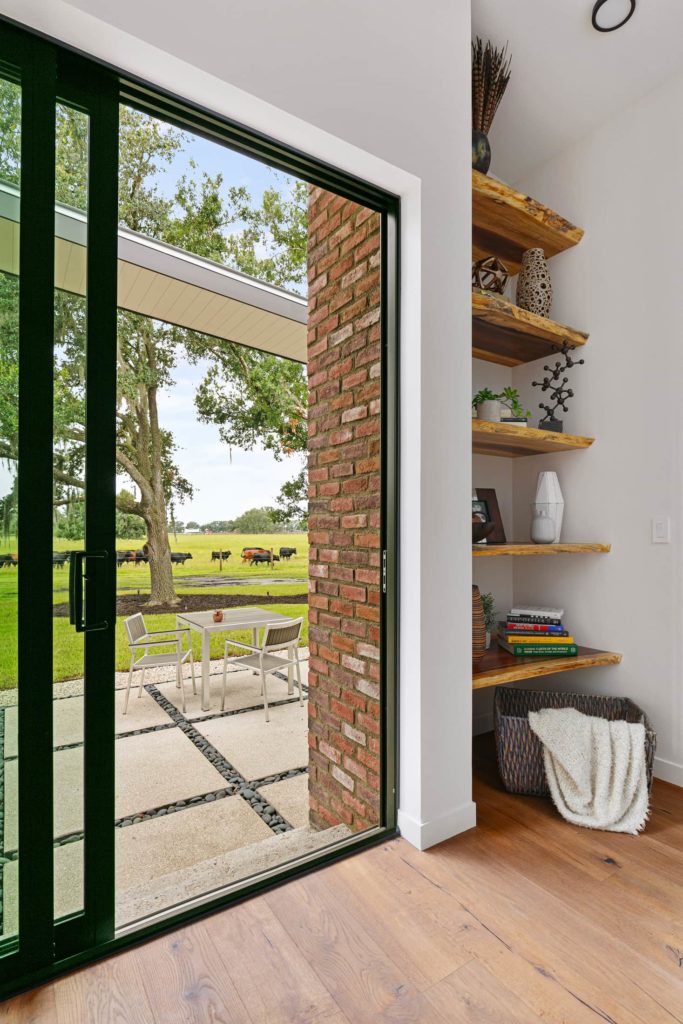
Tiny Gems in Concrete
Tiny houses are a niche that has been identified as a natural for precast concrete components. Superior Concrete Products of Euless, Texas, recently opened a tiny-home division, the Original Concrete Tiny House Co., to market diminutive dwellings built with the company’s steel-reinforced modular concrete panels.
According to Todd Sternfeld, CEO and owner of Superior Concrete, the tiny homes are available with various exterior finishes that duplicate the look of wood, brick, stucco, or stone. Six floor plans are offered, with five ranging from 150 to 600 square feet plus a 2,000-square-foot modular building that can be customized as a larger home, stable, or other structure.
It’s a bit early to make predictions about the success of Superior’s effort, but their tiny homes have a lot going for them. They are modestly priced, compact, durable, energy efficient, low maintenance, and look like traditional homes. As weather around the world grows more extreme and unpredictable and economic forces challenge housing attainability, buyers who are typically shut out of the market (think young first-timers and retirees) may find an alternative in pre-cast dwellings.
Schechter points out that precast concrete is a more expensive system than standard wood framing, which might hinder its wide acceptance in the homebuilding industry. “But I think there will always be those that want the benefits precast concrete offers,” she says.
Post by Susan Bady, self-proclaimed “armchair architect” and advocate of sustainability, new building technology and most of all, good design.